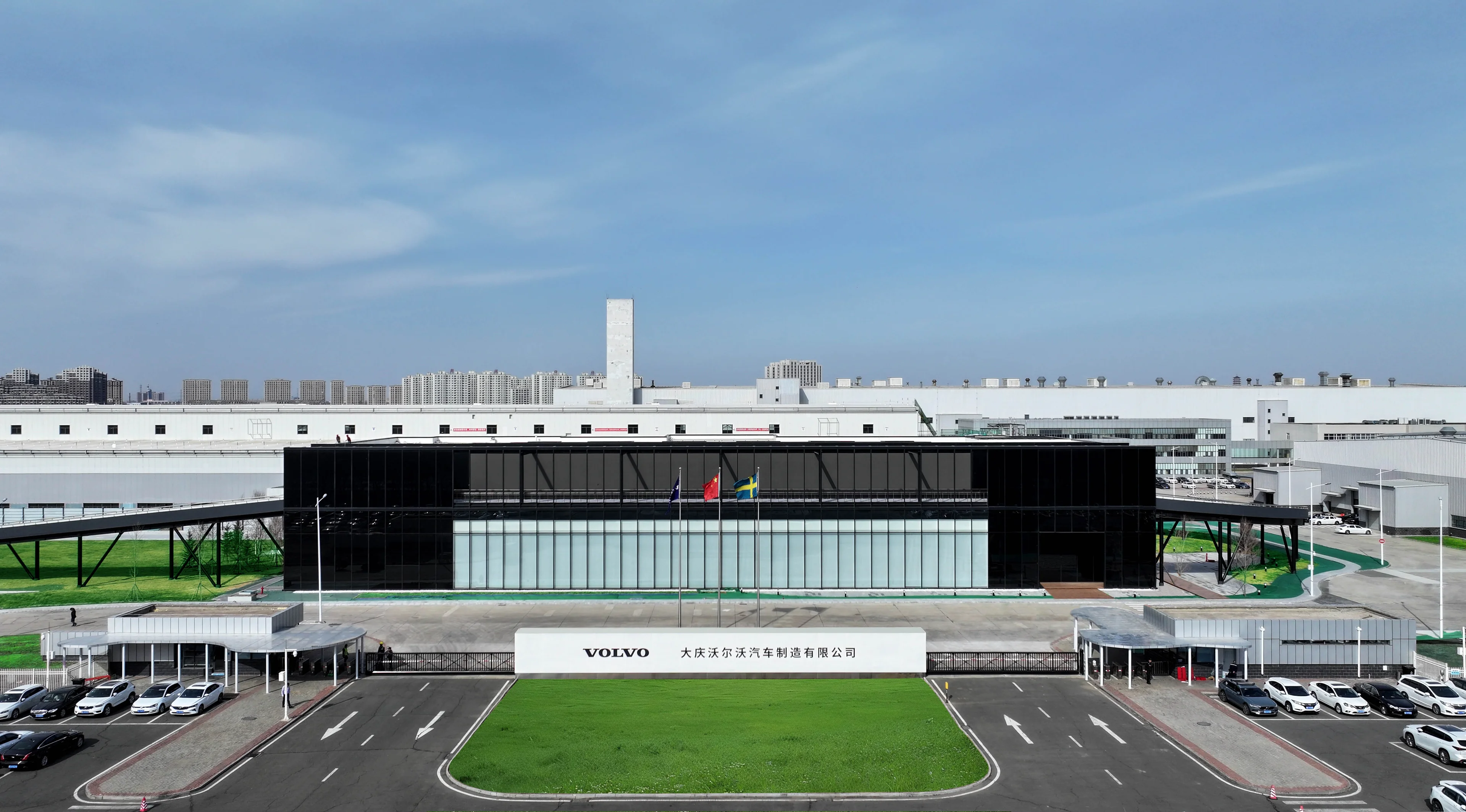
沃尔沃汽车大庆工厂于2013年9月正式落成,工厂位于黑龙江省大庆市龙凤区,厂区内设有冲压、焊装、涂装和总装四大整车制造车间,同时建有物流中心和质量检测设施,拥有完整的整车制造工艺链和严苛的质量管理体系。作为沃尔沃S90全球唯一的制造基地,沃尔沃汽车大庆工厂在规划、建设和生产过程中,严格秉承沃尔沃汽车生产制造系统(VCMS),遵循沃尔沃汽车全球统一采购、制造、技术和品质标准,拥有精准的规范化生产流程,世界一流的工艺技术以及严苛的质量管控体系,充分体现了沃尔沃汽车“中国制造 全球品质”的承诺和实力。
沃尔沃汽车大庆工厂
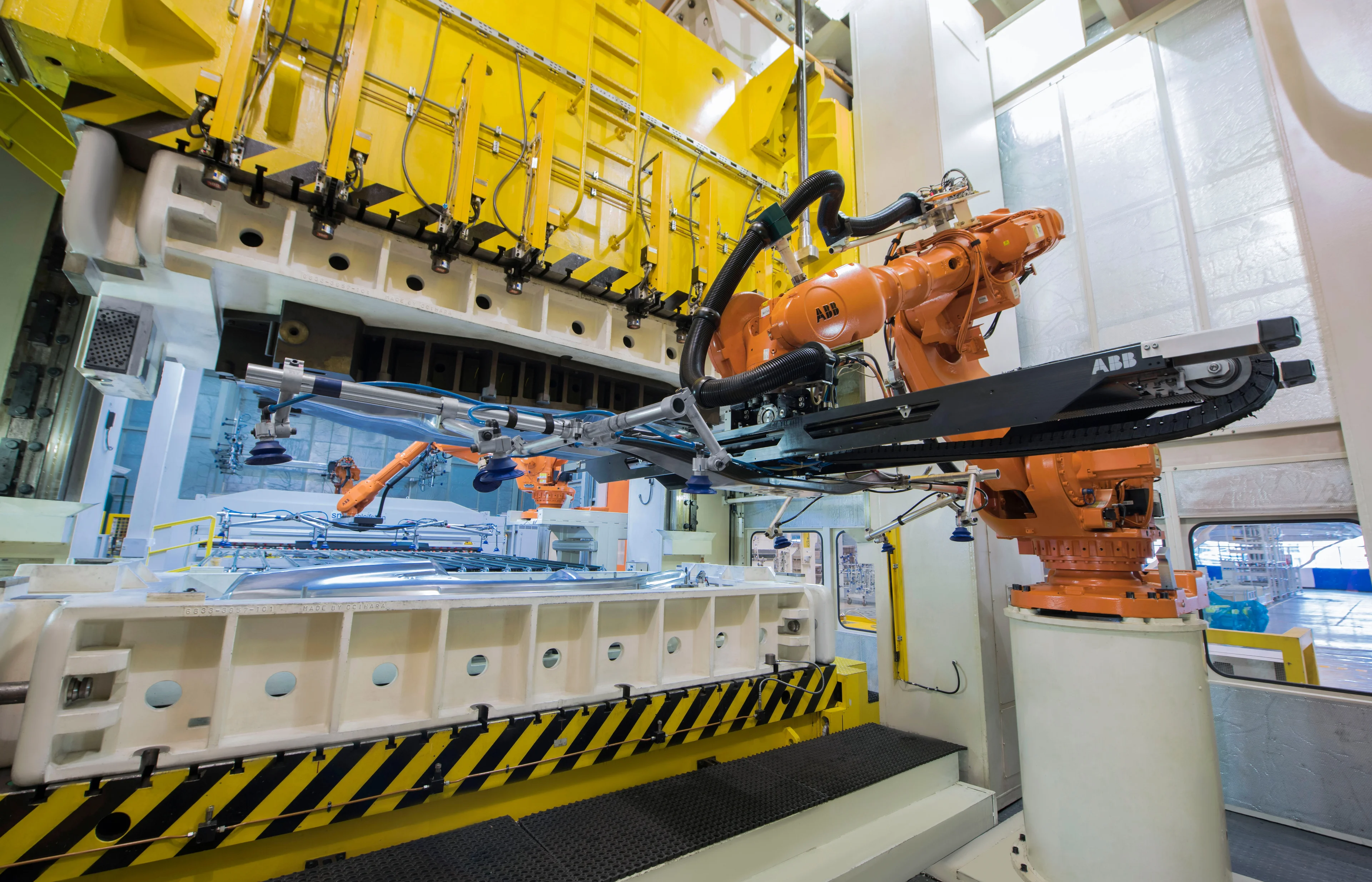
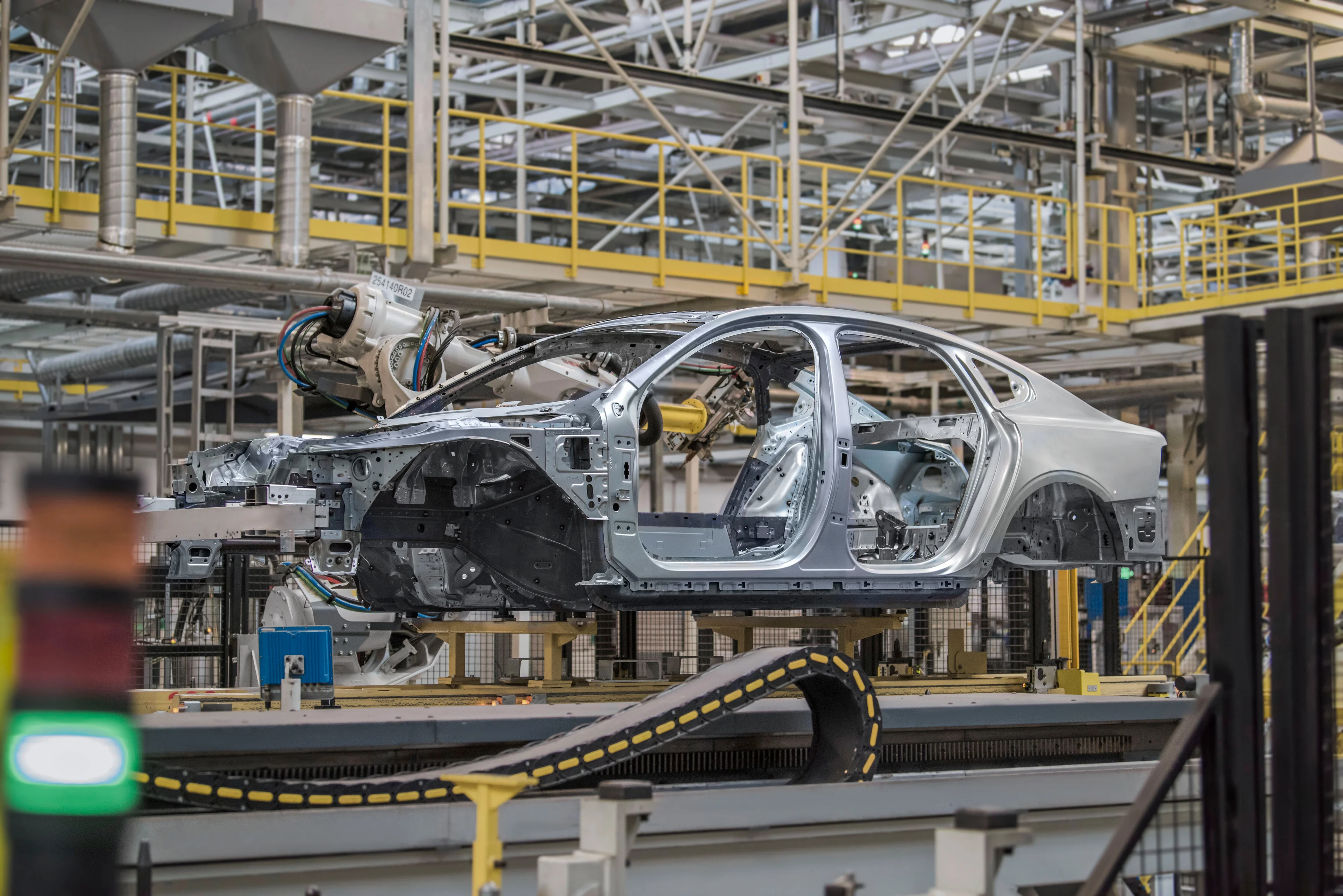
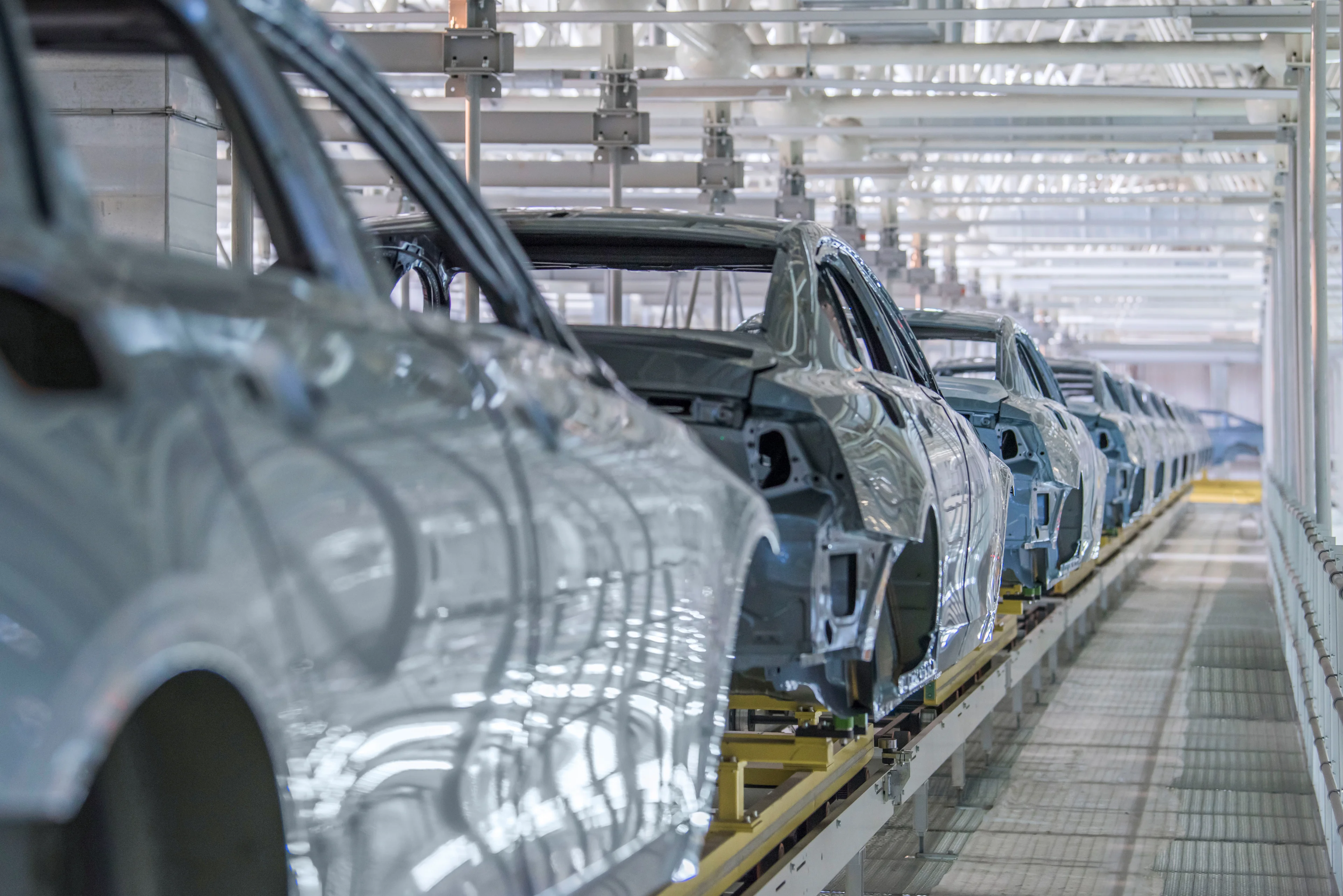
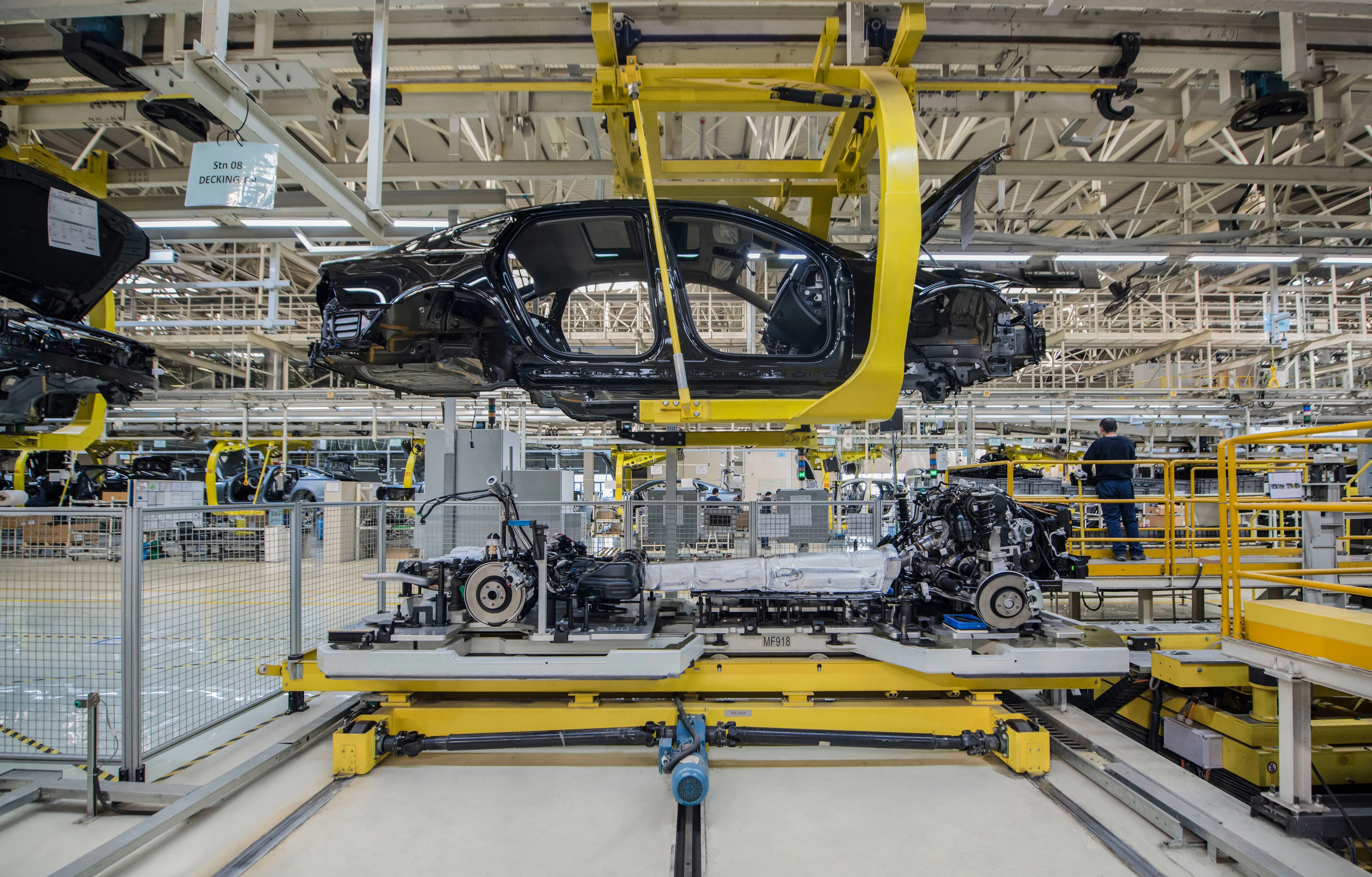
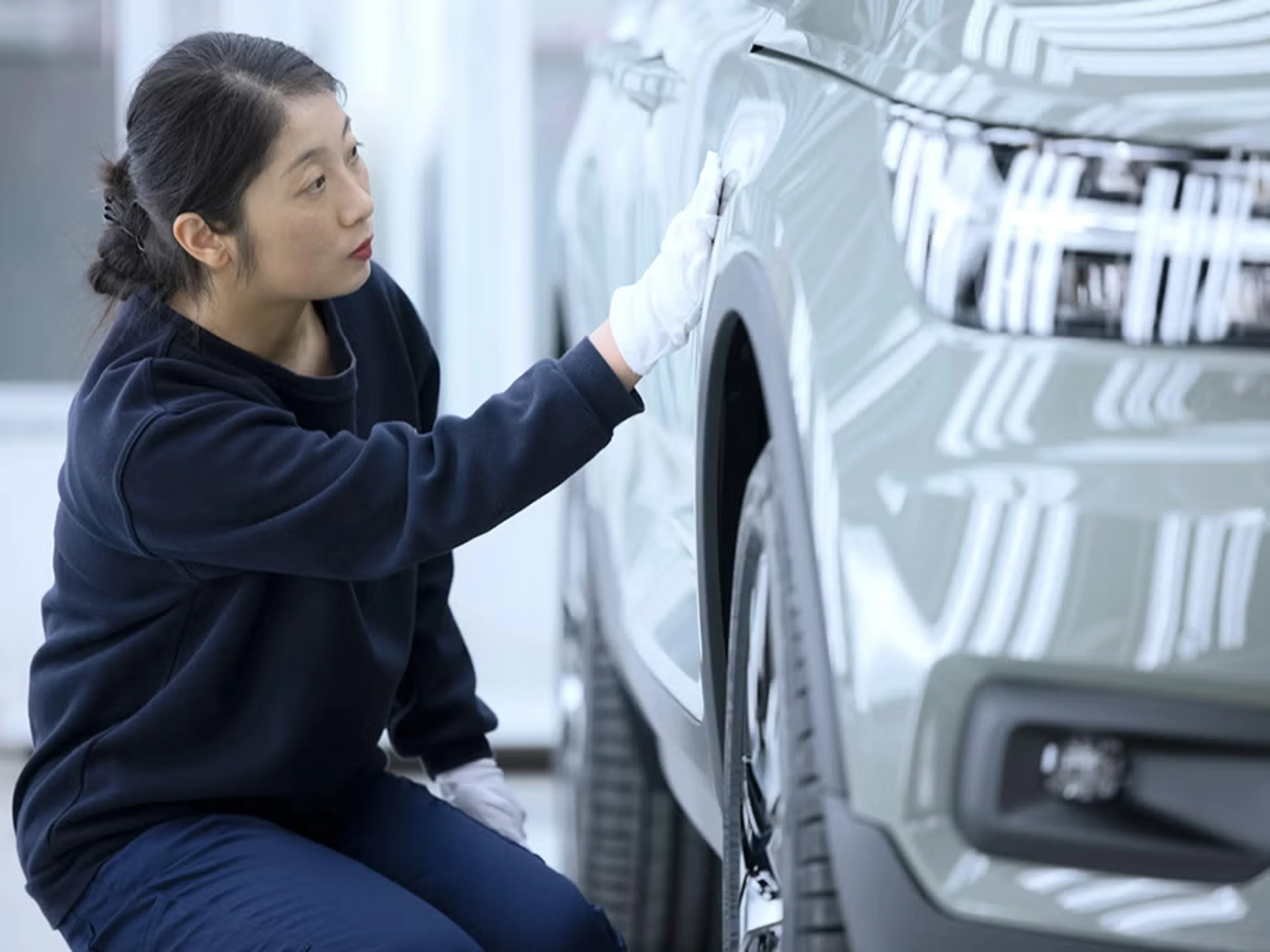
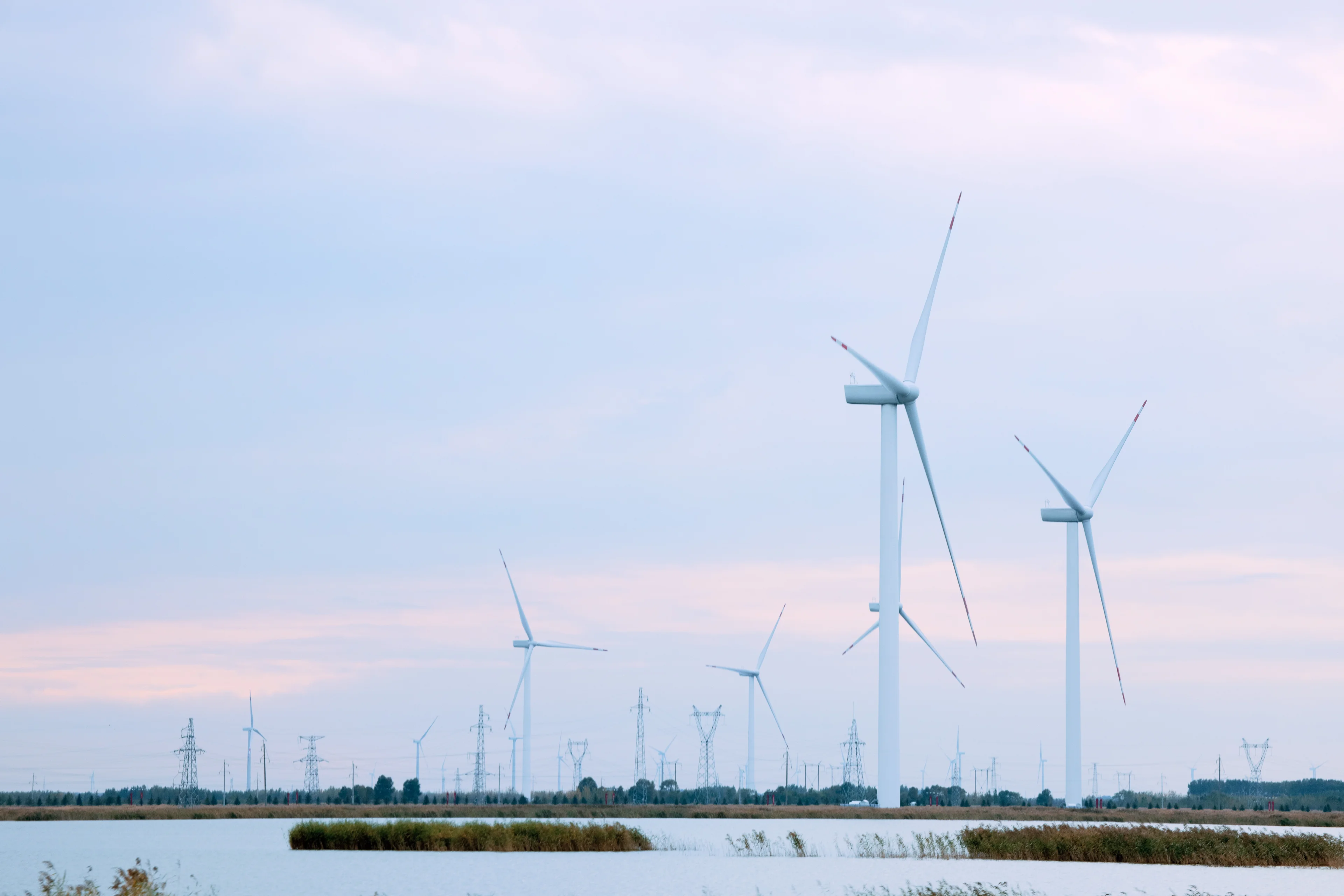
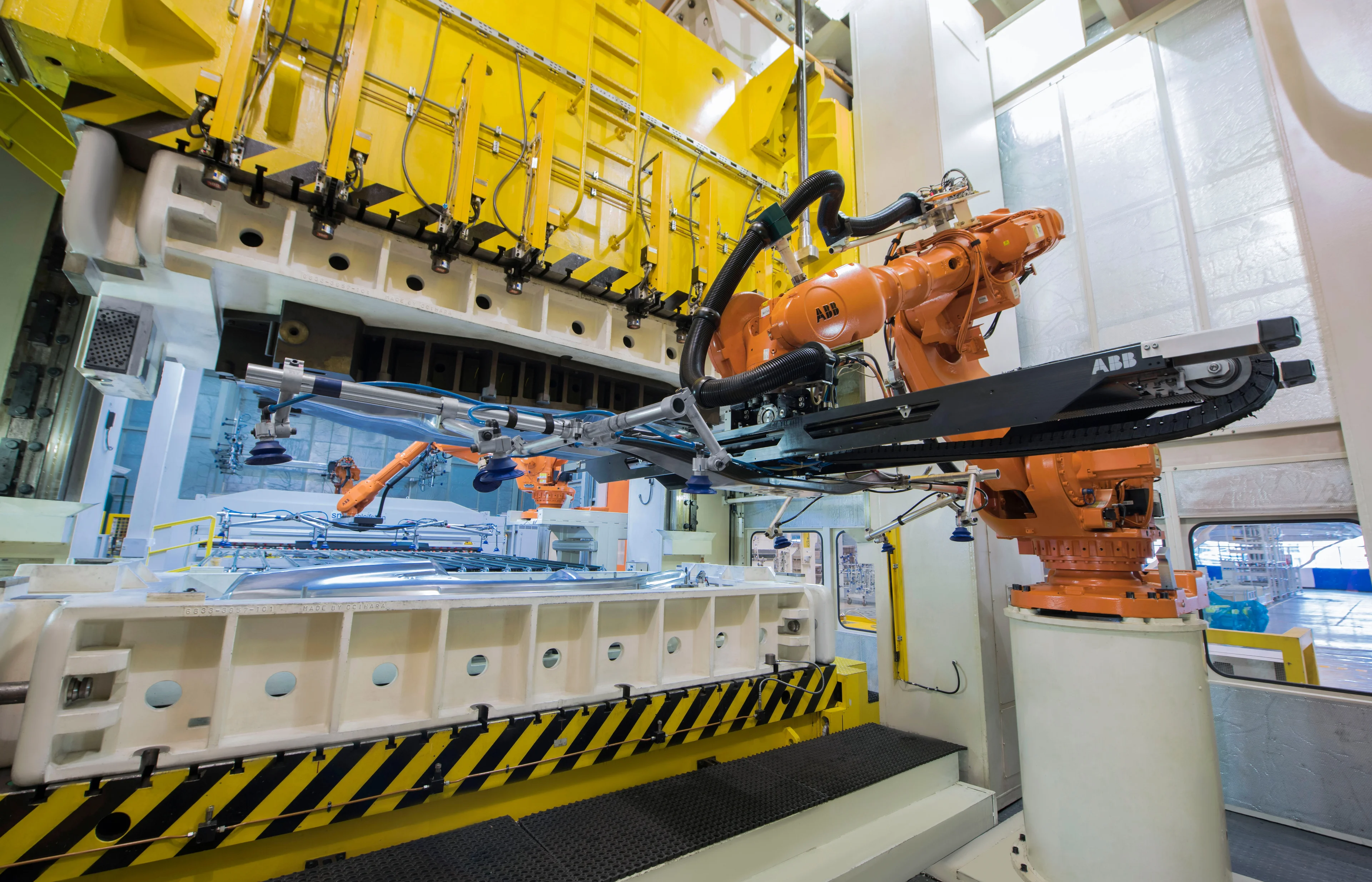
冲压车间
冲压车间作为生产制造的首道工序,也是高品质的起点。沃尔沃汽车广泛采用双面镀锌钢板,该材料具有耐腐蚀和使用耐久性的特点,同时具备良好的延展性和抗动态冲击能力。冲压车间整线配备5台四点机械式压力机,完成拉延、修边、冲孔、整形、翻边五道工序,部件搬运全部使用ABB直线7轴机器人。冲压生产线自动化率100%,实现充分的自动化与柔性化。同时,配备先进的钢、铝混合生产线,可以同时冲压钢板和铝板,结合世界级高精度模具,可确保零件精度控制在±0.5mm内,提升了车身结构件的一致性,为整车品质打下基础。
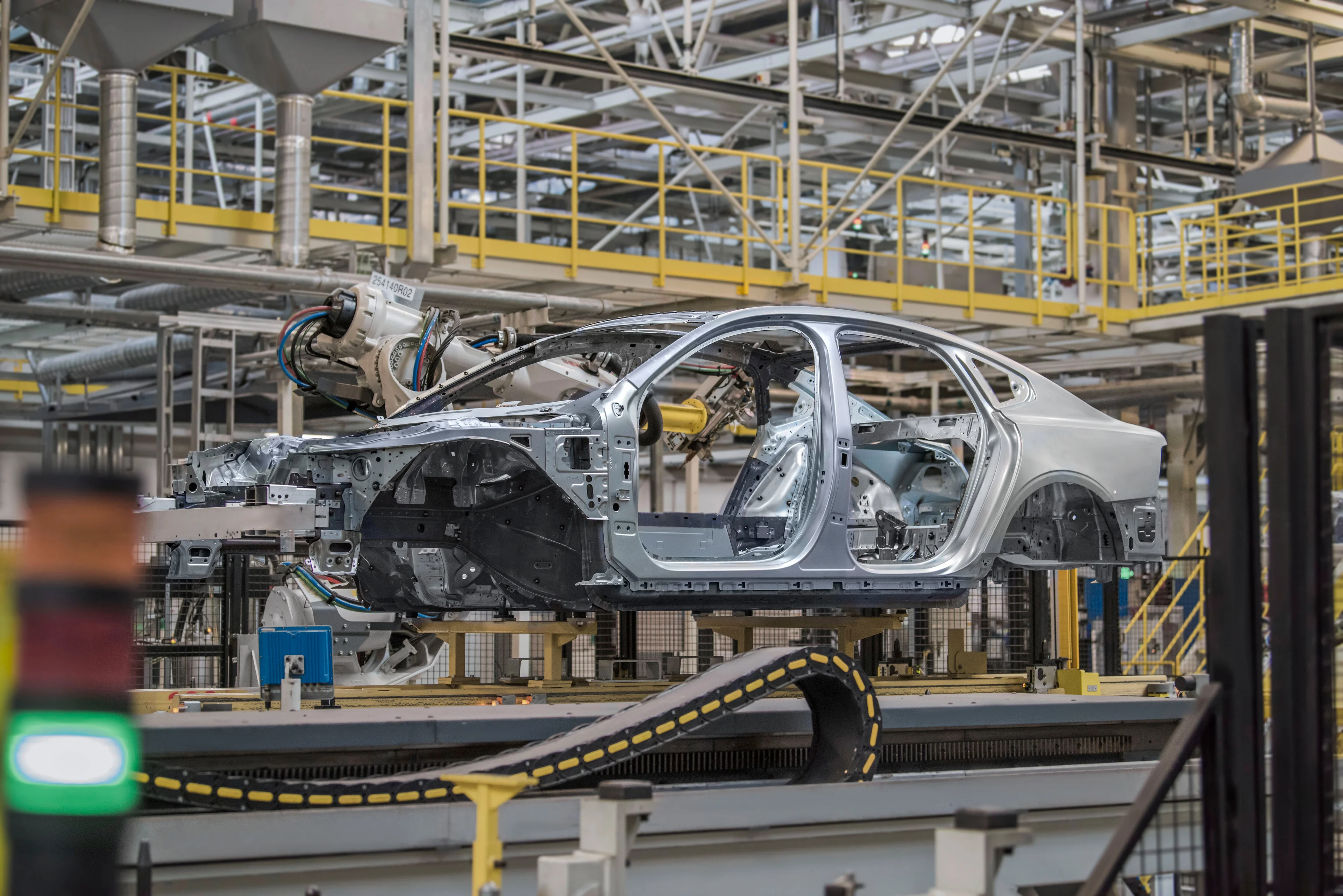
焊装车间
焊装车间是将冲压好的各种车身部件,通过焊接工艺连接在一起的过程。为了保证焊接工艺的精准性,焊装车间大量采用了自动化生产线,拥有347台ABB机器人。沃尔沃汽车采用大量硼钢材料,作为热成型超高强度钢,其屈服强度高达1600MPa。由于硼钢与其他材质焊接难度较大,沃尔沃汽车采用特别打造的“自适应焊接控制系统”,由“高精度焊接控制器”和“高科技焊钳”协同组成,可实时监测板材厚度,并据此计算和调整电流和通电时间,实现精准补偿,确保每一个焊点在焊接精度、牢固度和平整度都达到全球统一品质标准。针对铝材的连接,沃尔沃汽车采用航空级自冲铆接工艺,为车身提供更好的强度、扭转刚度和抗腐蚀性,提升车身安全性能。此外,在车顶、侧围、四门两盖等关键区域,沃尔沃汽车采用自动化激光焊接工艺,其焊接速度更快,不仅提升焊缝的美观和光洁度,也显著增强了车身结构关键部位的连接强度和整体刚性。
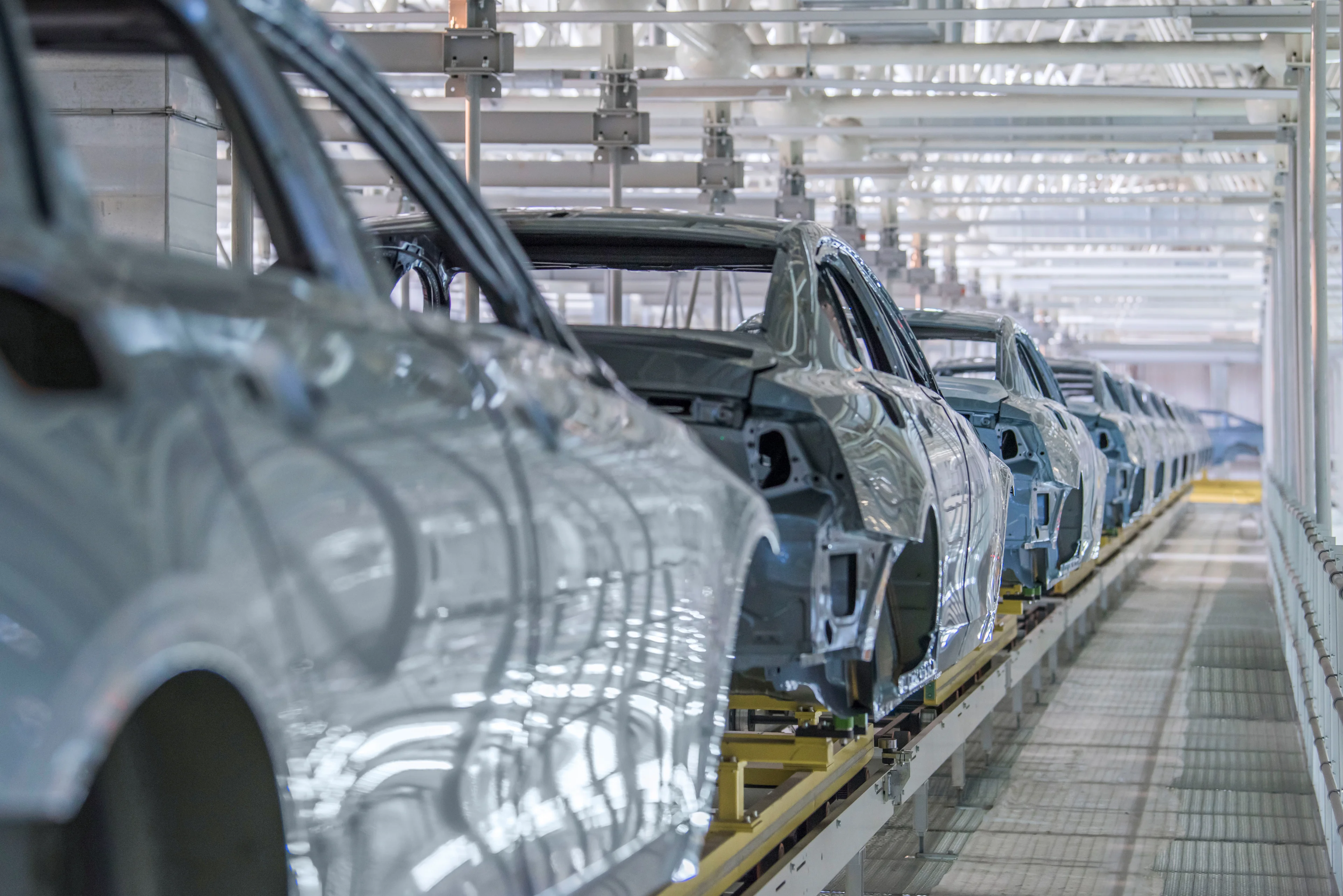
涂装车间
完成焊接的白车身将会进入涂装车间,主要工艺有预处理电泳、中涂、面漆、涂胶、整理报交等,工艺设计参照沃尔沃汽车全球质量控制流程和生产管理流程,拥有自动化机器人44台。 沃尔沃汽车对车身的防腐性能有着非常高的要求,其漆膜厚度为110微米,处于行业领先水平,可实现极端恶劣环境下的12年防腐,远超国家标准要求的10年防腐。为确保漆面品质达标,车身需经过共计16道防腐密封工序,全方位密封涂胶,四层涂层,三次高温烘烤和三重质检关卡,层层把控提升防腐耐久性。此外,沃尔沃汽车采用的巴斯夫电泳CathoGuard防腐技术,具有优化边缘保护、流动性和高泳透力等出众特质,可改变钣金表面物理属性,达到最佳防腐蚀性。
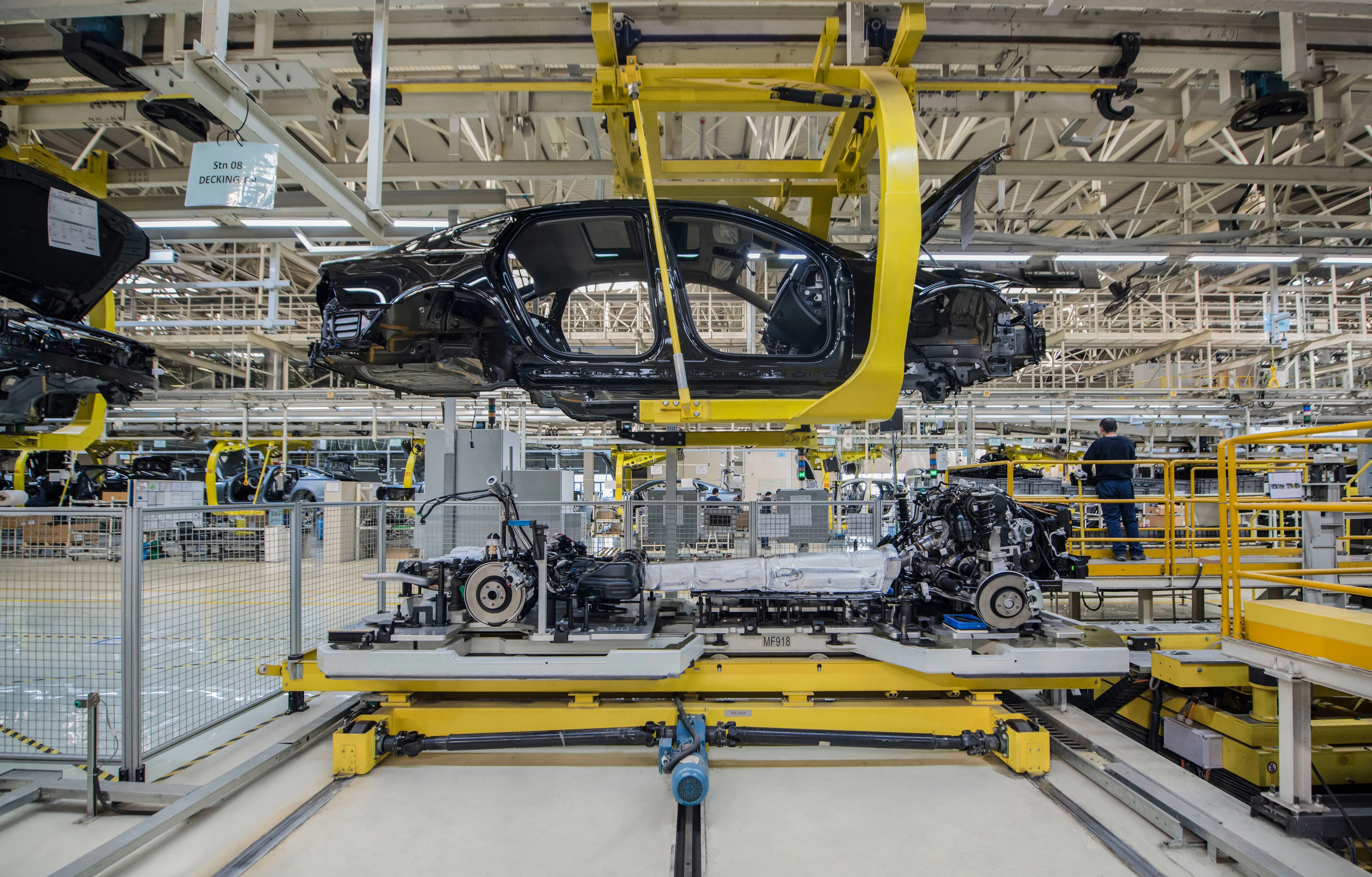
总装车间
总装车间是汽车制造的最后一个阶段,数千个零部件将会在这里组装完成一辆整车。总装车间100%采用电动拧紧工具。在拧紧过程中,电动工具可以控制和记录每一颗螺栓的拧紧力度、扭矩等,保证工艺精准的同时,所有关键螺栓的拧紧信息终身可追溯。在车身与底盘的合装工位(俗称“结婚工位”),底盘上60颗不同规格的螺丝实现 “一体式自动合装”,确保不同规格的螺栓被同步一次性100%自动化拧紧,完成底盘与车身的合体。该工艺不仅大大减轻了操作员人工拧紧所造成的身体负担,也确保装配过程中每一个螺丝受力均匀,并最大限度地减少了车身的装配应力,提高驾驶稳定性。
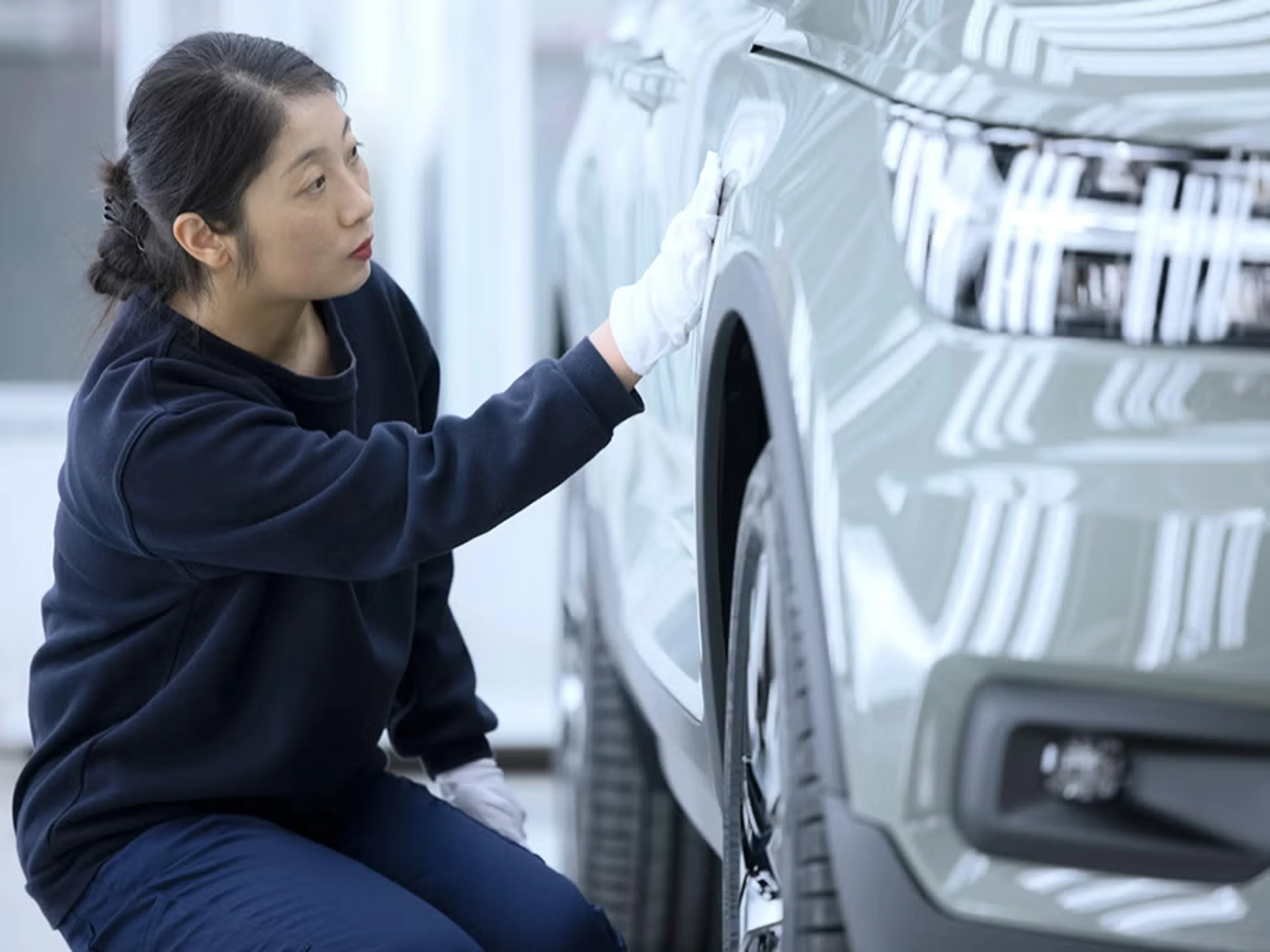
质量把控
沃尔沃汽车秉承严苛的质量标准和管理体系,从前端采购环节,到冲压、焊装、涂装、总装的整个生产流程,始终贯穿执行7层次质检体系,全过程把控产品品质。
• 第一层 供应商品质检测
• 第二层 冲压品质检测
• 第三层 焊装品质检测
• 第四层 0瑕疵漆面检测
• 第五层 总装品质检测
• 第六层 整车品质检测
• 第七层 消费者视角全感官检测
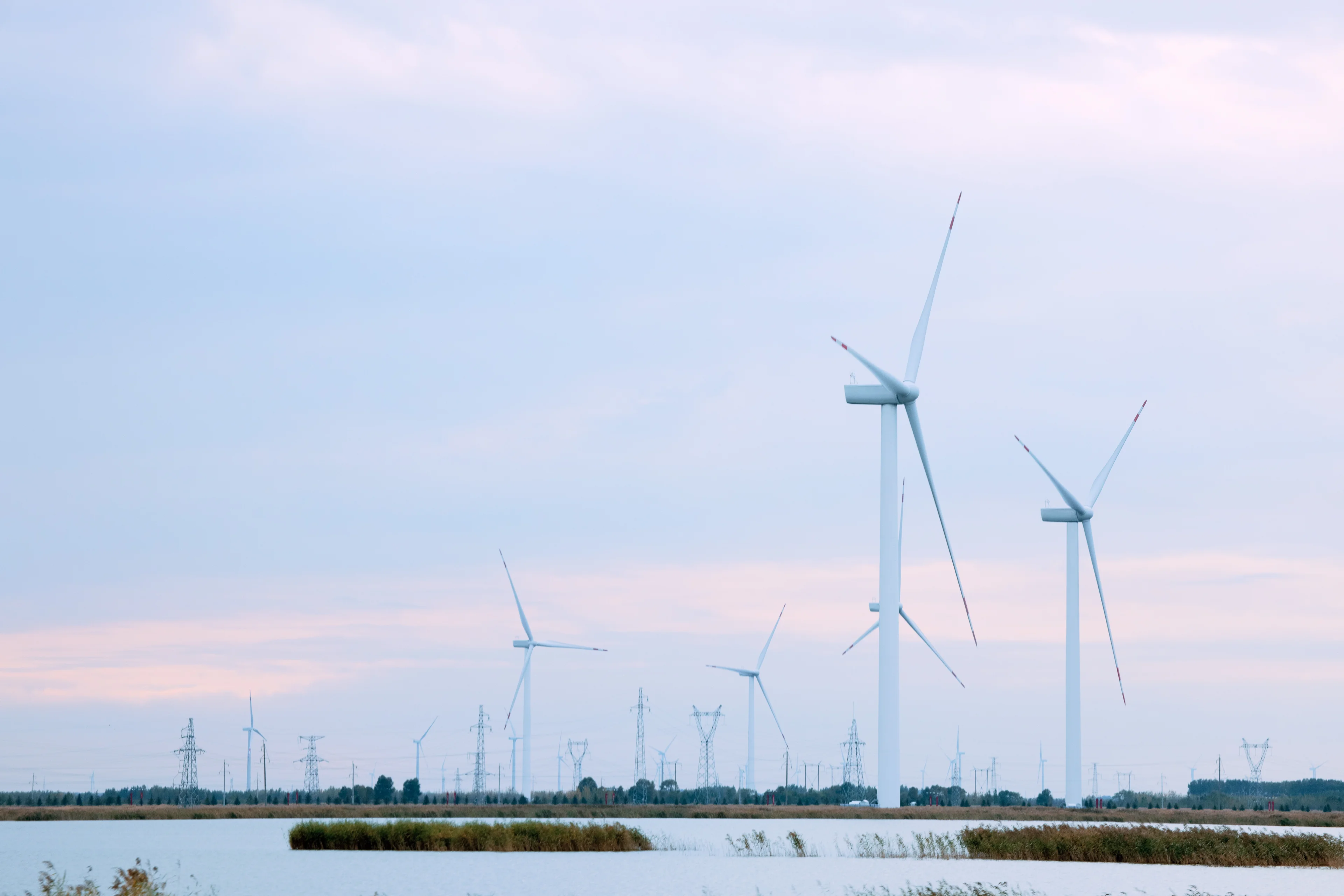
环保行动
大庆工厂严格执行“工业污水一级排放标准”,是全国少数达到该标准的整车制造基地。工业废水经过多道净化工序处理后,不含一类重金属,年回收中水超过300吨,废水回用率达40%。车间内还能见到净化后的废水养鱼场景,直观体现废水处理的高标准与环保成效。此外,大庆工厂还积极推动绿色能源转型,率先采用生物质气替代天然气作为能源来源,减少碳排放的同时,也促进可再生能源在制造环节的应用。
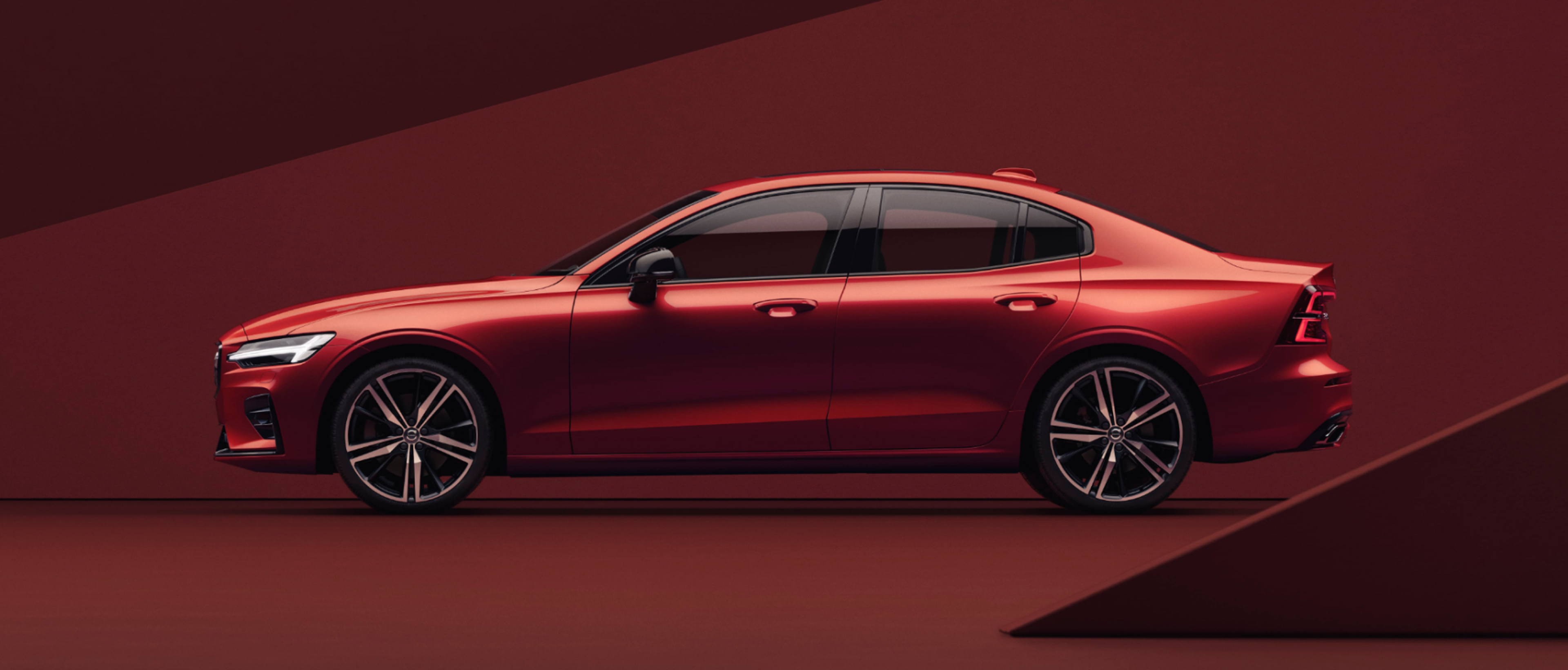
相关数据
占地面积833,000平方米,规划产能15万辆/年,生产车型沃尔沃S90、S60。
工厂荣誉
2019年获评工信部“国家级绿色工厂”。
2021年获评黑龙江省首个实现电能零碳排放的制造基地 。
2021年获评智能工厂认证。
2022年获评大庆市无废企业。
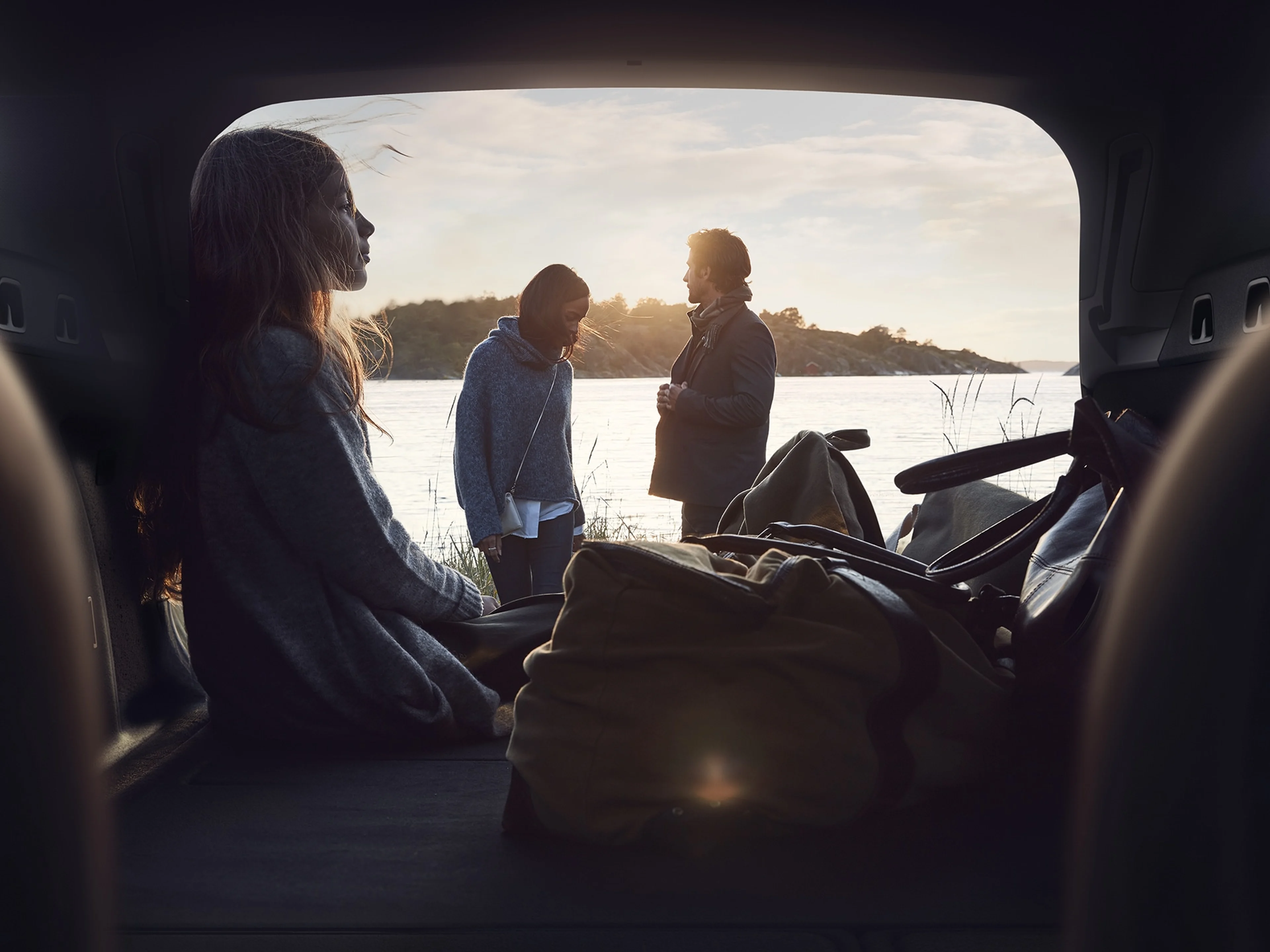